Современные технологии переработки изношенных автопокрышек и других резино-технических отходов
Опубликовано Редактор 26-07-2003 (7766 прочтений)В мире ежегодно производится 15-20 млн тонн автопокрышек и других резино-технических изделий. Срок эксплуатации этих изделий невелик, и в течение года они превращаются в отходы. На полигонах и свалках уже накопилось около двух миллиардов изношенных покрышек, и с каждым годом их количество непрерывно увеличивается. При этом основные компоненты изделий - резина, синтетический корд и металлическая проволока — практически не отличаются по молекулярной структуре и свойствам от исходного состояния. Все эти компоненты пригодны для повторного использования.
Казалось бы, открываются прекрасные возможности: надо быстрее начинать переработку этих отходов, чтобы получать прибыль в размере не менее 10 млрд долларов в год. Но тут происходит самое странное. Отходы либо собирают и уничтожают в печах, либо выбрасывают в овраги, на свалки и т.д. Почему это происходит? Потому, что многочисленные разработанные в разных странах методы переработки резино-технических изделий либо экологически небезопасны, либо неэффективны с экономической точки зрения.
А методов переработки было разработано очень и очень много.
Изношенные покрышки используют при создании подводных рифов с целью разведения рыбы и моллюсков, а также при укреплении береговой полосы от размывов. Шины целиком или отдельными сегментами вводят в массивные бетонные изделия с целью экономии цемента. Из шин делают заборы или укрепляют ими земляные откосы. Из разрезанных на полосы, а затем сшитых друг с другом автопокрышек получают листовой кровельный материал, похожий на шифер, однако, основные способы утилизации шин и других резино-технических изделий основаны на сжигании, разложении, девулканизации и измельчении.
Сжигание отходов резины
Резина является горючим материалом, а ее теплотворная способность такая же, как у каменного угля. Однако при сжигании выделяется много сажи, сернистых газов и других токсичных продуктов. Приходится уделять большое внимание очистке отходящих газов, а это требует больших затрат. В большинстве случаев шины сжигают в цементных печах — при этом выделяется значительно меньше сернистых газов. Но и коэффициент полезного действия цементных печей очень низкий. Чтобы увеличить КПД приходится нарезать шины на мелкие кусочки, использоватьспециальные печи с хорошим поддувом и другими приспособлениями. А это снова удорожает процесс.
Как показывают проведенные расчеты, сжигание шин и других резиновых изделий всегда убыточно, а себестоимость получаемой при этом электроэнергии существенно выше, чем при сжигании обычного каменного угля.
Следует, помнить, что при сжигании уничтожаются потенциально ценные продукты — резина и синтетический корд. Нетрудно придти к выводу, что сжигать резиновые отходы в цементных или в каких-либо других специальных печах, оборудованных системами очистки газов, могут позволить себе только те страны, которые выделяют очень большие средства на поддержание экологической чистоты.
Разложение резины
Применение разного рода катализаторов — масел, расплавов солей, битумов и т.д. — позволяет разлагать резину на низкомолекулярные газообразные, жидкие и твердые продукты. Процесс удается осуществлять в вакууме или в инертной атмосфере.
Лет 20-30 тому назад к этим процессам проявляли очень большой интерес. Сейчас он в значительной степени угас: предлагаемые методы оказались неэкономичными. Выделение ценных продуктов разложения резины, их очистка, утилизация образующихся при этом вредных продуктов - все это требует слишком больших расходов. Значительно проще и дешевле получать те же самые ценные продукты из обычной нефти.
Девулканизация резины
При производстве резиновых изделий их подвергают вулканизации, т.е. сшивают макромолекулы каучуков межмолекулярными, в большинстве случаев серными, связями. Поэтому с научной точки зрения именно девулканизация - термическое разрушение межмолекулярных связей - кажется наиболее обоснованным методом переработки изношенных резиновых изделий. Во второй половине двадцатого века этот метод был весьма популярен. Для его осуществления было изготовлено большое количество специализированных установок - девулканизаторов. Однако постепенно стало ясно, что методу присущи слишком серьезные недостатки, устранить которые не удается.
Переработка отходов резины в девулканизаторах протекает слишком медленно и сопровождается выделением большого количества токсичных газов. И, главное, - при девулканизации разрушаются не только межмолекулярные, но и внутримолекулярные связи. Снижается молекулярный вес каучука и, как следствие, ухудшаются основные свойства получаемого продукта.
Введение девулканизата в первичную сырую резину существенно снижает прочность и деформируемость получаемых из таких смесей резиновых изделий. Поэтому в абсолютном большинстве стран применение в вулканизации резиновых отходов бы прекращено. И, хотя в последние годы предложены новые методы девулканизации, позволяющие избирательно разрушать именно межмолекулярные серные связи, полностью подавить дестукцию молекул каучука все равно не удается.
Измельчение резиновых отходов
При измельчении резины ее молекулярная структура и основные свойства сохраняются в наибольшей степени. Они сохраняются даже тогда, когда из отходов получают высокодисперсные порошки с размером частиц менее 0,5 мм.
К настоящему времени разработано и запатентовано огромное количество способов измельчения резины. Они основаны на разрушении, ударном и взрывном воздействии. Резину измельчаю, продавливая ее под большим давлением через мелкие отверстия. Измельчают воздействием электрических разряде или ударными волнами, воздействием лазера или электронного пучка и т.д. Эти методы применяют в очень широком температурном интервале - от -2С до +300 °С.
Каждый из методов имеет свои преимущества и свои недостатки, характеризуется разной величиной удельных энергозатрат и позволяет получать разные по размеру и форме резиновые частицы. Однако специфика механического разрушения резины такова, что при различных (но слишком высоких) значениях температуры, измельчение приводит к образованию резиновых частиц со слишком гладкой поверхностью. Это обстоятельство являете общим недостатком многих методов измельчения, существенно ограничивая область вторичного использования получаемых порошков.
В первую очередь это присуще низкотемпературным методам измельчения, с помощью которых удается получить наиболее однородные и мелкие частицы, напоминающие по внешнему виду битое стекло. Такие частицы имеют очень низкую адгезию к сырым резинам и большинству полимерных термопластов. Они плохо растворимы в битуме, плохо сорбируют нефтепродукты. Введение таких порошков в сырые резины существенно снижает свойства получаемых резиновых изделий. Поверхность таких изделий выглядит слишком неровной, шероховатой. Где же используют такие порошки?
Как ни странно, в США их преимущественно сжигают в топках тепловых электростанций! Сжигают, несмотря на то, что удельные энергозатраты на получение криогенного резинового порошка достигают 1000-2000 кВт.ч/т (около 200 кВт.ч/т требуется на измельчение и 800-1800 кВт.ч/т - на получение необходимого количества жидкого азота). Конечно, об экономической целесообразности процесса такого измельчения говорить не приходится. Для его осуществления необходимы очень большие дотации государства. Например, в США фирмы, занимающиеся криогенным измельчением, получают жидкий азот и соответствующее оборудование по сниженным ценам.
Более крупные резиновые частицы (от 0,5 до 3 мм), получаемые измельчением при нормальных температурах, применяют только для изготовления материалов типа линолеума, с использованием в качестве связующего полиуретанового клея, или резиновых плит и других листовых материалов, в которые приходится вводить достаточно большое количество серы, пластификаторов и других добавок. С коммерческой точки зрения применять резиновую крошку при изготовлении таких материалов не слишком целесообразно.
Понимая это, в США и ряде европейских стран уже более 40 лет ведутся работы, направленные на то, чтобы сделать поверхность криогенных резиновых частиц менее гладкой. И за счет этого существенно расширить область применения резиновых порошков. С этой целью порошковые частицы подвергают воздействию различного рода факторов, способствующих девулканизации приповерхностного слоя: импульсный нагрев частиц перегретым паром, нагрев излучением лазера, облучение частиц гамма-лучами с последующей прививкой на поверхность различного рода мономеров, нанесение на поверхность частиц порошковой серы и других низко-молекулярных веществ, обеспечивающих разрушение низкомолекулярных связей при нагреве и т.д.
В целом ряде случаев такая химическая обработка резинового порошка приводит к неплохим результатам. Однако она заметно увеличивает стоимость резинового порошка. Поэтому с экономической точки зрения ее применение становится нецелесообразным.
По существу, только методы высокотемпературного сдвигового измельчения позволяют при сравнительно низких энергозатратах получать высокодисперсные, химически активные порошковые резины, пригодные для изготовления широкого круга коммерчески-ценных вторичных материалов и изделий.
Высокотемпературное сдвиговое измельчение резиновых отходов
Метод высокотемпературного сдвигового измельчения (ВСИ) был разработан в ИХФ РАН им. Н.Н.Семенова в содружестве с ГАНГ им. И.М.Губкина, ИСПМ РАНиТашГУ еше в начале 80-х годов. Метод ВСИ тесно связан с явлением множественного растрескивания твердых полимеров и резин в условиях интенсивного сжатия и деформации сдвигом.
Когда сдвиговое деформирование осуществляют в камере под воздействием оптимальных значений давления и температуры, множественное разрушение протекает достаточно интенсивно и завершается быстрым разрушением материала на отдельные частицы, т.е. образованием порошка. При этом основное количество порошковых частиц образуется не около металлических стенок камеры, окружающих слой перерабатываемого материала, а внутри самого слоя. Происходит как бы взрывное самоизмельчение перерабатываемых материалов, как жестких, так и упругих. В некоторых, более ранних работах это явление — быстрое разрушение и измельчение материалов в интенсивном силовом поле — получило название "реологический взрыв".
Как правило, с ростом температуры скорость сдвигового разрушения материалов возрастает. У любого полимера или полимерного композита существует температурный интервал, в котором сдвиговое измельчение протекает наиболее эффективно с образованием высокодисперсного порошка при минимальных энергозатратах. Обычно ширина таких интервалов не превышает 200 °С, а их положение зависит от типа полимера, содержания наполнителей, пластификаторов, от наличия в полимере межмолекулярных связей и от целого ряда других факторов. Большинство аморфно-кристаллических термопластов наиболее эффективно измельчаются методом ВСИ в температурной интервале предплавления, когда степень кристалличности полимера составляет от одного до десяти процентов. Эффективное измельчение резин начинается при тех температурах, когда начинается термоактивированный распад межмолекулярных связей: изопреновых резин - при 150-180 °С, резин на основе этилен-пропиленового каучука — при 210-230 °С и т.д.
К преимуществам метода ВСИ следует отнести то, что:
- Метод эффективно применяют при оптимально высоких температурах, когда удельные энергозатраты на измельчение минимальны, а применение других методов измельчения практически исключено.
- Метод позволяет получать очень тонкие порошки с размером частиц от 10 до 500 мкм и с большой удельной поверхностью.
- Метод обеспечивает возможность тонкого измельчения таких материалов, как сверхвысокопрочные арамидные волокна, отходы "теплого линолеума", шелуха гречихи, отходы пенополиуретана, пенополистирола, куски автопокрышек вместе с синтетическим и металлическим кордом и т.д., которые другими методами практически не измельчаются.
- Поскольку при измельчении методом ВСИ молекулярная структура практически не разрушается, или разрушается в слабой степени, получаемые порошки могут быть использованы в дальнейшем в качестве полноценного сырья.
Можно указать и другие преимущества, однако и отмеченных вполне достаточно, чтобы понять, насколько перспективна данная технология.
Уже в самом начале 80-х годов для реализации метода были использованы двухшнековые экструдеры: экструдеры типа ZSK, ZE и аналогичные им. Эти экструдеры неплохо зарекомендовали себя при измельчении термопластов, резин и других сшитых полимеров. При переработке резиновых отходов в таких экструдерах измельчение начинается в микроучастках, расположенных в точках зацепления кулачков и затем постепенно распространяется на весь объем перерабатываемого материала. Поскольку в экструдере обычно используют две или несколько зон измельчения, расположенных последовательно, то значительная часть порошковых частиц, образовавшихся в первой зоне, подвергается затем сжатию, монолитизации и повторному разрушению. Это, естественно, увеличивает общие энергозатраты.
Другим недостатком экструдеров является неэффективный отвод тепла из зоны измельчения, что снижает максимальную производительность. В работе фирмы "Берсдорфф" (Германия) для увеличения отвода тепла из экструдера была использована система из вертикально расположенных колонн, в которых нагретые до 140-150 °С порошки охлаждались воздушным потоком и затем снова загружались в экструдер для дополнительного измельчения. Такое конструктивное решение существенно увеличило стоимость установки. Поэтому многолетняя разработка подобных экструдеров завершилась изготовлением и испытанием одного контрольного образца.
В дальнейшем для реализации сдвигового измельчения в России были разработаны установки роторного типа - роторные диспергаторы (Рис.1), обеспечивающие измельчение полимеров в непрерывном, одностадийном режиме.
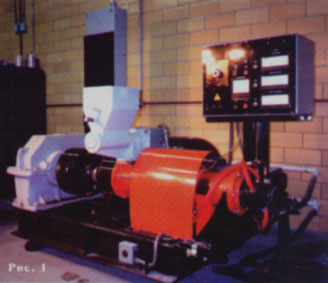
Современный промышленный диспрегатор состоит: из блока измельчения, представляющего собой цилиндрический корпус с загрузочным отверстием и выгрузным патрубком; расположенного внутри этого корпуса вращающегося шнека - ротора, блока дозированной подачи измельчаемого материала; системы охлаждения ротора и корпуса камеры оборотной водопроводной водой и пульта управления.
Блок измельчения включает в себя камеру сжатия и быстрого разогрева перерабатываемого материала и камеру быстрого охлаждения полученного порошка. Собственно измельчение осуществляется в сравнительно узкой зоне, расположенной на стыке камер, между неподвижной стенкой корпуса и вращающимся элементом тонкого измельчения, выполненным в форме короткого ротора или тела вращения. Образующийся перед измельчающим элементом плотный, практически монолитный слой материала подвергается быстрому сдвиговому нагреву до критической температуры и разрушению. Образующиеся при этом порошковые частицы охлаждаются в следующей камере. Представляют интерес следующие параметры процесса:
- Блок измельчения диспергатора, обеспечивающего сдвиговое измельчение резины с производительностью 130-200 кг/час, имеет сравнительно небольшие габариты.
- Расстояние между загрузочным и выгрузным патрубками составляет всего 60-80 см.
- Ширина зоны измельчения не превышает 4 см.
- Время прохождения материала через зону измельчения составляет 0,5-3 с.
- Скорость нагрева материала в первой камере достигает нескольких градусов в секунду, а скорость охлаждения порошковых частиц во второй камере может составлять 5-1 градусов в секунду.
Таким образом, переработку и измельчение осуществляют в режиме импульсного или "шокового" нагрева с последующим очень быстрым охлаждением или закалкой. В этом режиме удается получать уникальные частицы дискретно-девулканизированной резины размером 30-800 мкм. Каждая такая частица состоит из множества микроблоков резины размером не более 20 мкм, окруженных слоем девулканизованного или частично девулканизованного материала. В пределах каждой порошковой частицы все входящие в нее микроблоки связаны друг с другом проходными макромолекулами или проходными тяжами из резины с частично разрушенной сеткой межмолекулярных связей. Удельная поверхность порошка составляет 0,3-2,5 м2г.
Получение активных порошков дискретно девулканизированных резин
Как показали исследования, содержание растворимой фракции в таком порошке выше, чем у исходной резины, но не более, чем на 10-20 вес.%. Иначе говоря, переработка отходов в роторном диспрегаторе приводит к дискретной девулканизации резины одновременно с ее измельчением.
По данным электронной микроскопии на поверхности порошковых частиц такой дискретно девулканизованной резины находится большое количество микрокристаллов серы. Вероятно, это обстоятельство обуславливает высокую химическую активность получаемого в диспергаторе резинового порошка. Если отдельную частицу или состоящий из частиц слой поместить между металлическими пластинами и подвергнуть прогреву в условиях сжатия, то происходит самовулканизация. В результате, получаются тонкие резиновые пластинки с очень гладкой поверхностью.
Уникальность рассматриваемых порошков проявляется также в том, что частицы дискретно-девулканизированной резины, введенные в сырые резиновые смеси того же химического состава, играют роль агентов вулканизации. В частности, введение в сырую резиновую смесь со стандартным содержанием серы измельченных в диспергаторе резиновых отходов приводит к увеличению скорости девулканизации в 1,5-2,5 раза. Измельченные отходы вводили даже в каучуки, вообще не содержащие серы, и даже в этом случае после прогрева под давлением образовавшейся смеси удается получать резины, если содержание порошка превышает 20 вес.%.
Интересные результаты были получены при исследовании физико-механических свойств вторичных композитных резин, полученных на основе смеси первичной сырой резины с измельченными в диспергаторе отходами того же химического состава. Как было показано специалистами нашего Института, Института авиационных материалов (Москва), фирмы "Тайя Интернейшнл" (США) и специалистами других фирм, прочность и деформируемость таких композитных резин в целом ряде случаев превышает прочность и деформируемость первичных резин, если содержание порошка составляет 3-20 вес.% (Рис.2). При дальнейшем увеличении содержания порошка прочность и деформируемость несколько снижаются, но затем при содержании порошка выше 70% веса эти параметры снова увеличиваются и могут превысить соответствующие параметры первичных резин.
Аналогичные результаты получены при исследовании широкого круга резин на основе изопренового, дивинильного, бутадиен-стирольного, этилен-пропиленового, фторсодержащего и других каучуков.
Следует подчеркнуть, что измельченные в диспергаторе резиновые отходы можно вводить в сырые резиновые смеси без какой-либо дополнительной химической модификации. В совместной работе со специалистами фирмы "Тайя Интернейшнл" (США) мы специально исследовали этот вопрос. Полученные в диспергаторе резиновые порошки на основе этилен-пропилен-диенового каучука были разделены на две партии. Первую партию вводили в сырую резину без какой-либо дополнительной модификации. Вторую партию порошка подвергали принятой в США процедуре модификации и затем вводили в сырую резиновую смесь.
Путем серной вулканизации смесей были изготовлены композиционные резины и исследованы их свойства. Как видно из приведенных в таблице 1 данных, модификация не оказала сколь-нибудь заметного влияния на свойства получаемых композитных резин, а в некоторых случаях даже привела к ухудшению свойств. Это обстоятельство является достаточно важным с коммерческой точки зрения, т.к. модификация заметно увеличивает себестоимость получаемого порошка.
Остановимся теперь на еще одном важном обстоятельстве: при сдвиговом измельчении наряду с образованием высокодисперсного порошка образуется определенное количество более крупных, монолитных частиц, которые по своей структуре и рельефу поверхности практически не отличаются от резиновых частиц, получаемых при более низких температурах, в т.ч. при криогенных. Средний размер частиц дискретно-девулканизованной резины составляет обычно 150-250 мкм, средний размер более крупных монолитных частиц -1-2 мм. Для последующего использования эти частицы, необходимо разделить (попадание крупных монолитных частиц в композитные резины приводит к ухудшению их физико-механических свойств).
В реальной практике разделение двух типов частиц осуществляют путем просеивания на вибросите с размером ячеек 0,6 или 0,9 мм. Оставшиеся на сите крупные монолитные частицы можно либо использовать отдельно, например, при изготовлении резиновой плитки, либо повторно измельчать, пропуская их через диспергатор.
При измельчении отходов в роторном диспергаторе содержание высокодисперсного порошка дискретно-девулканизированной резины обычно составляет 75-90 вес.% от общего количества переработанного материала (остальное составляют монолитные, неразмолотые частицы). При измельчении тех же отходов в двухшнековом экструдере содержание порошка дискретно-девулканизированной резины несколько ниже, причем оно очень сильно зависит от типа экструдера. В отдельных случаях измельчение в экструдере позволяет получать всего 10-30 вес.% высокодисперсного порошка.
Рассмотрим теперь основные процессы переработки и измельчения шинных отходов. Специфика этого производства определяется тем, что при изготовлении автопокрышек используются резины нескольких типов, в том числе, трудноизмельчаемые резины. Наряду с этим, автопокрышки содержат значительное количество металлического и синтетического корда (до 30 вес.%). Разделить в процессе измельчения разные типы резин — это задача будущего. Однако, отслоить всю резину от корда и потом разделить материал на основные компоненты — резину, металлическую проволоку и полиамидное волокна - необходимо. Это требуется для дальнейшего эффективного использования этих материалов.
Именно это и осуществляют на первом этапе переработки с помощью различного технологического оборудования и, в том числе, установок роторного типа. Подробно этот вопрос будет рассмотрен в следующем разделе.
Институт химической физики им.Н.Н.Семенова РАН
журнал "Вторичные ресурсы" №1 2002 год